Von Admin
2025-03-19 01:12:40
Die Kernpunkte und Ingenieurpraxis des Fahrzeug-Drahtgurtdesigns
Das Entwerfen von Kabelgurten ist ein entscheidender Engineering-Prozess, der eine sichere und effiziente elektrische Konnektivität in Fahrzeugen gewährleistet.
Als Schlüsseldesigner im integrierten Entwurf von Automobilelektroniksystemen beeinflusst das Layout-Design von Automobildrahtgurten direkt die elektrische Leistung und Zuverlässigkeit des gesamten Fahrzeugs. Als „neuronales Netzwerk" des Automobils müssen Verkabelungsgurte effiziente Verbindungslösungen für elektronische Geräte in komplexen Umgebungen erreichen. Im Folgenden werden die technischen Punkte von den Konstruktionsprinzipien bis zum gesamten Produktionsprozess ausführlich erläutert.
1. Grundprinzipien des Automotive Wiring Harness Design
- Sicherheitsdesign-Spezifikationen: Das Layout muss die Anforderungen an Brandschutz, Hitzebeständigkeit und Feuchtigkeitsbeständigkeit erfüllen und das Risiko von Kurzschlüssen und Erdfehlern vermeiden.
- Zu ver lä s sig keits garan tie für Fahrze ug dra ht gur te : Ho cht em peratur - und V ibr ations best än dige Dr äh te werden ausge wä hlt , um sich an extr eme Arbeits bedingungen von - 40 ° C anz upas sen und 125.
- Leichtes Layout des Automobildrahtgürts: Vereinfachen Sie die Länge und die Verbindungen des Drahtgürts, reduzieren Sie die Ausfallrate und die späteren Wartungskosten.
- Wartbarkeitstechnischer Standard: Modulares Design, kombiniert mit farbcodierten Etiketten für eine schnelle Wartung.
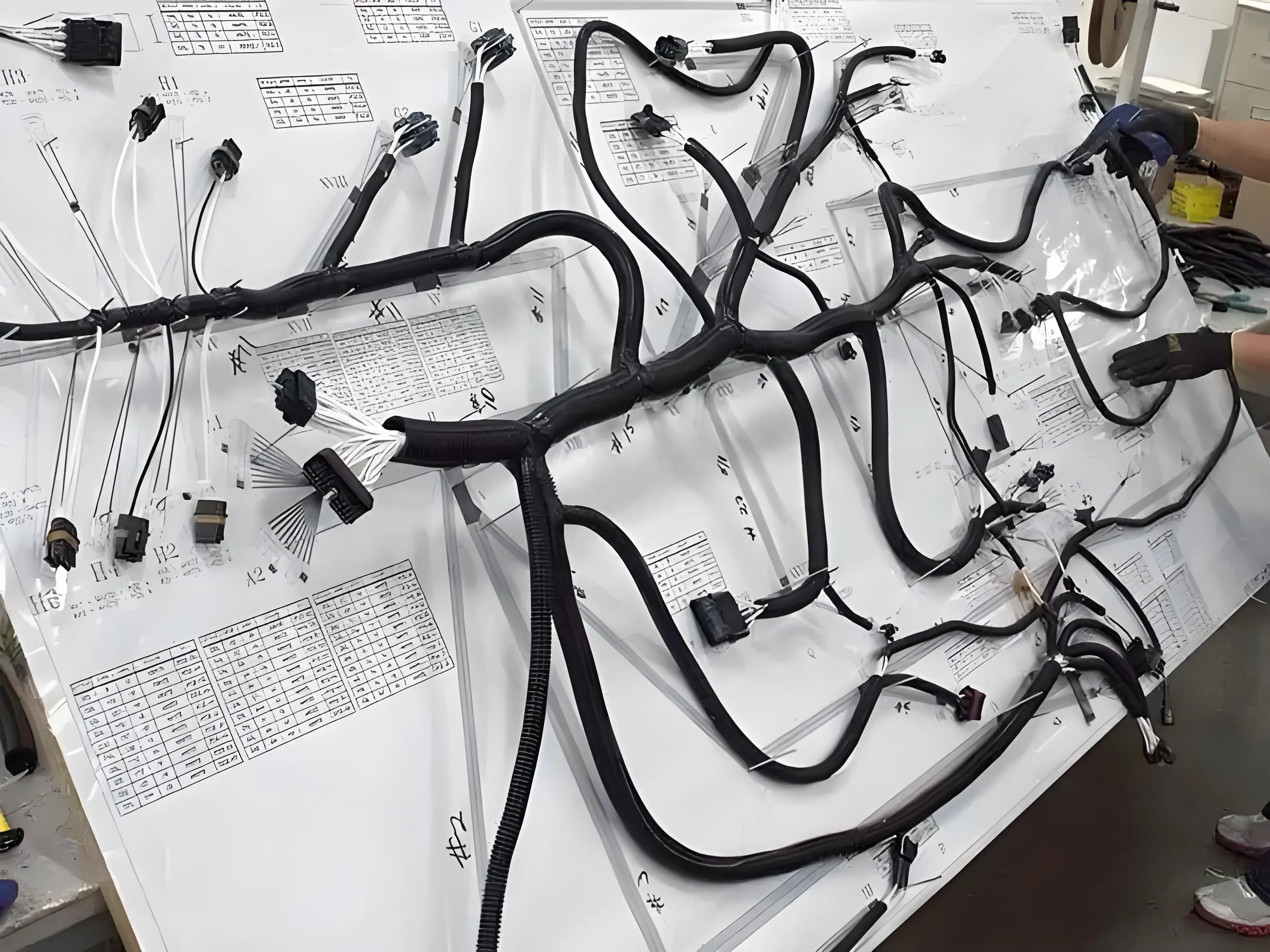
2. Optimierung der Automotive Wiring Harness Layout Strategie
- Entwurfsmethode für die Kabelung von Partitionen: In Bereichen wie dem Motorraum und der Kabine wird eine unabhängige Verkabelung verwendet, um Signalkreuzstörungen zu vermeiden.
- Elektromagnetische Verträglichkeit (EMV) - Schutztechnologie: Die Hochfrequenzsignalleitung verwendet eine zweischichtige Abschirmschicht und hält einen Abstand von mindestens 15 cm von der Stromleitung.
- Leichtgewichtslösung für die Verkabelung von neuen Energiefahrzeugen: Aluminiumdraht und dünnwandige Isoliermaterialien verwenden, wodurch das Gewicht im Vergleich zu herkömmlichen Kupferdraht um 30% reduziert wird.
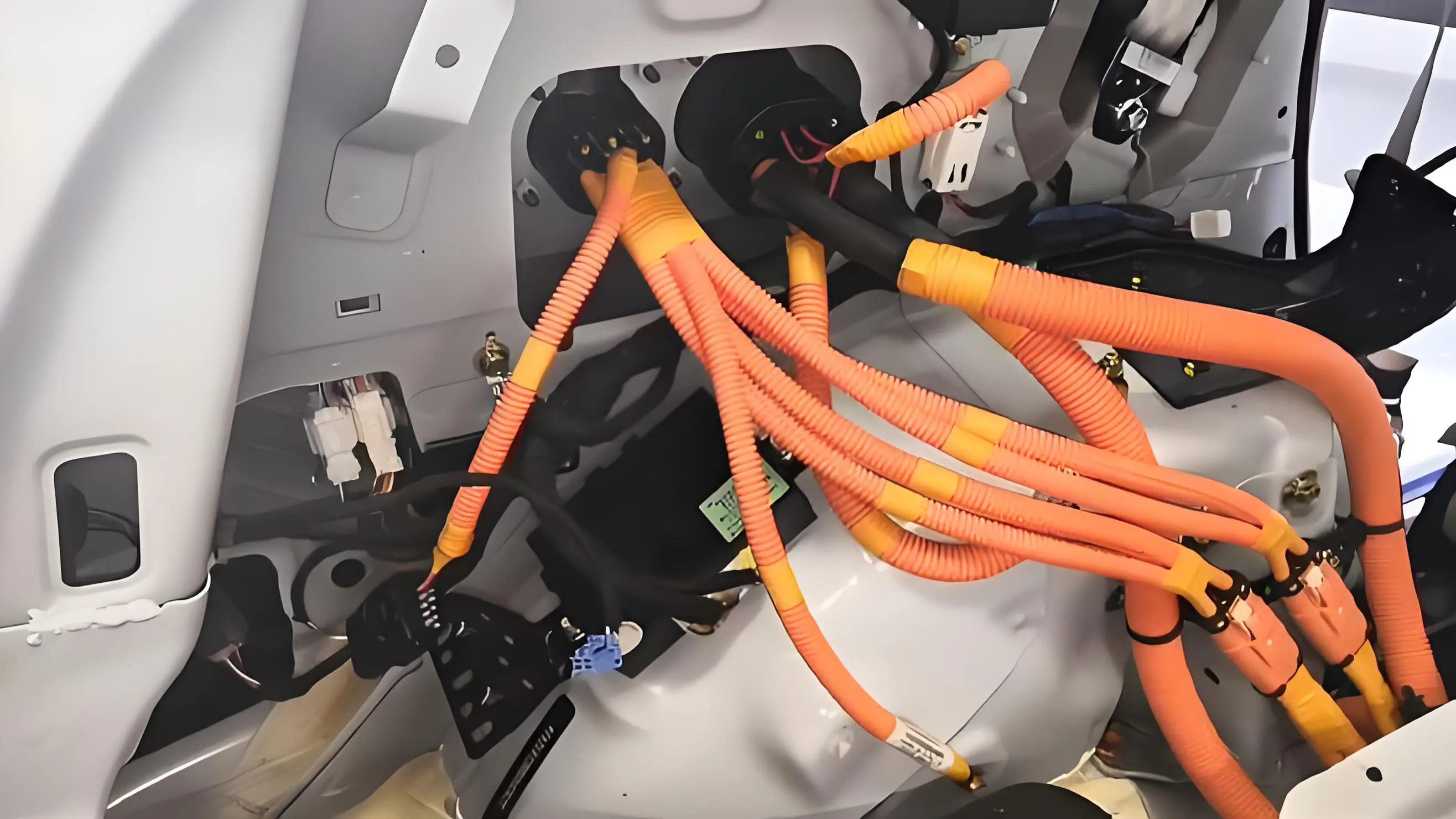
3. Wichtige Punkte für die Auswahl der Kernkomponenten von Fahrzeugdrahtgürteln
- Berechnung der Drahtspezifikationen für das Fahrzeugdrahtgurt: Passen Sie den Drahtdurchmesser anhand des Laststroms (z.B. 2,5 mm 2 Querschnittsfläche für ABS erforderlich).
- Wasserdichtes Design von Automobilsteckverbindern: Dichtungskomponenten aus der Qualität IP67 mit Schnappenbefestigung, um ein Vibrationslocken zu verhindern.
- Neues Energiefahrzeug Hochspannungsdrahtgürtsmaterial: Silikongummi-Isolierschicht kann hohen Temperaturen von 300 ° A standhalten und erfüllen die Anforderungen einer 800V-Spannungsplattform.
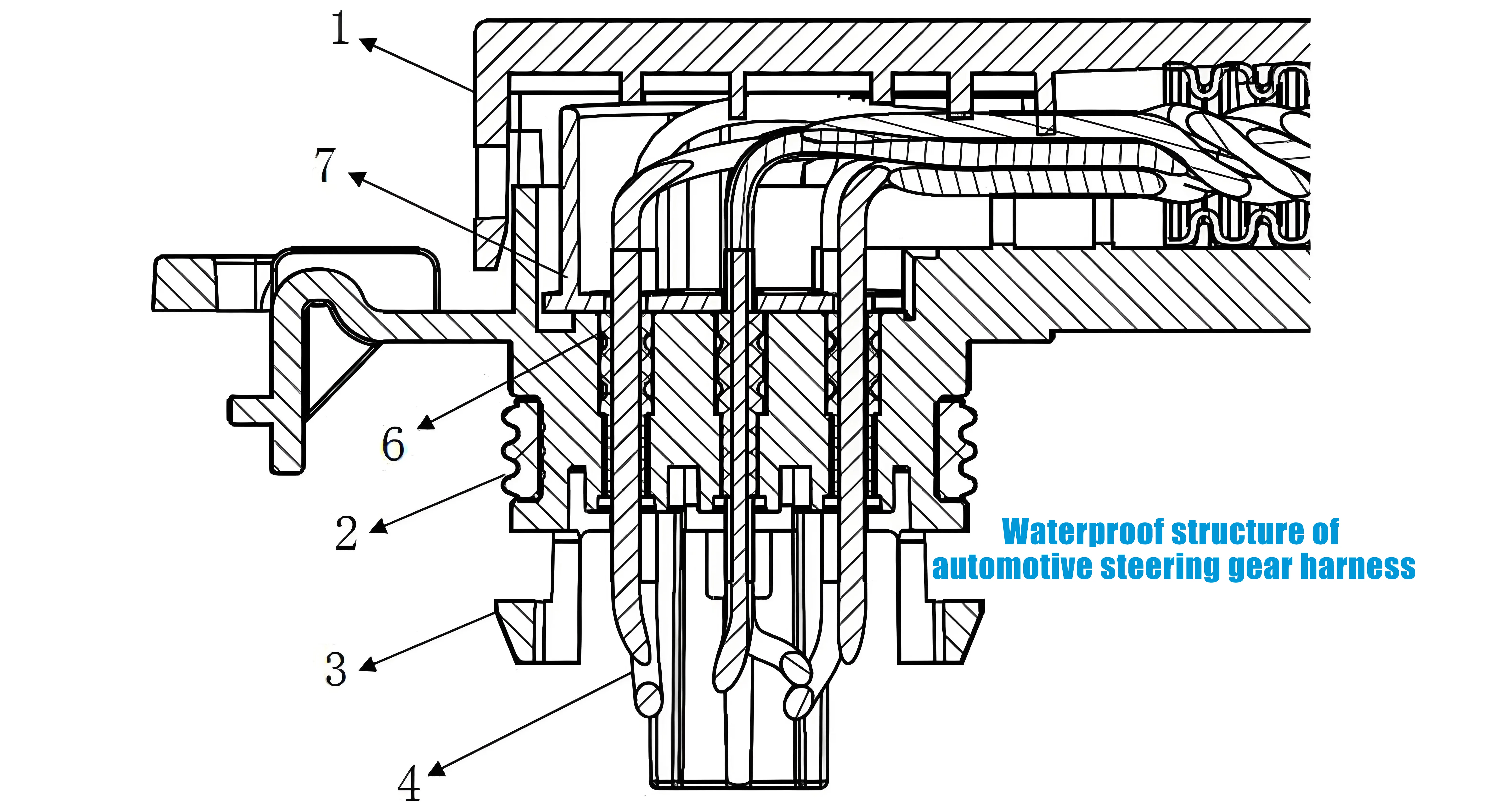
4. Komplette Prozessschritte für das Layout der Automobildrahtgurte
- Anforderungsanalyse der Fahrzeugelektrik: Erstellen Sie eine Stromverbrauchs - und Kommunikationsmatrix für Geräte wie ECU und Sensoren.
- 3D-Drahtgurtsimulation: Verwenden Sie die CATIA / CHS-Software, um die Rationalität des Weges zu überprüfen und Störungen durch bewegliche Teile zu vermeiden.
- Zuverlässigkeitsüberprüfung von Drahtgürtenproben: Durch strenge Experimente wie 100000 Ein - und Ausziehprüfungen und 50G-mechanische Stoßprüfungen.
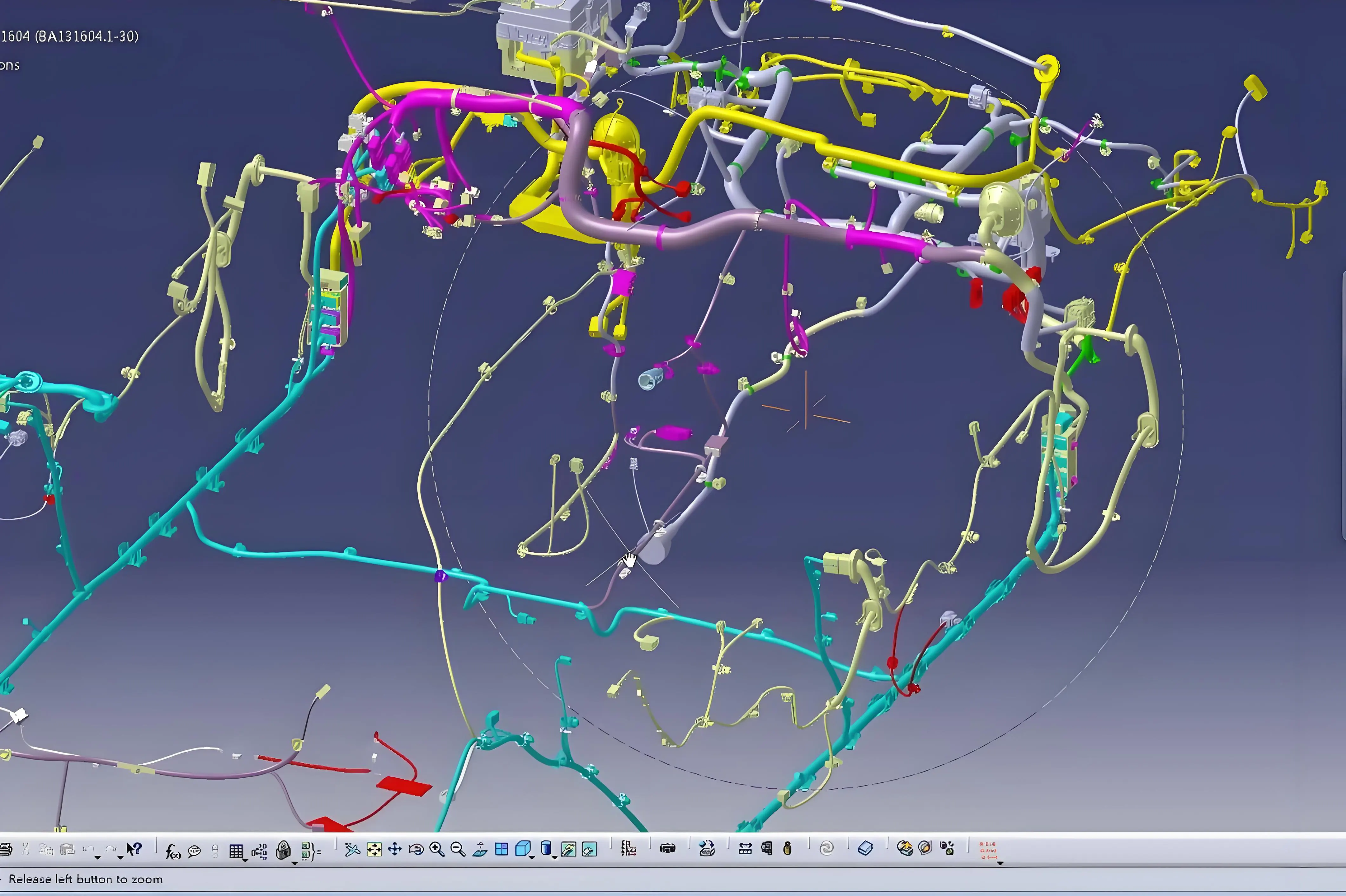
5. Schlüsselschritte im Automotive Wiring Harness Testing
- Automatisierte Erkennung der Leitungsimpedanz: Mit einem fliegenden Nadeltester erreichen Sie eine 100%ige Kontinuität-Screening.
- Hochspannungsdrahtgürts-Isolationsleistungstest: 500V DC widerstehen Spannungstest dauert 60 Sekunden, mit Leckstrom < 10mA.
- Debugging-Test für das elektrische System des Fahrzeugs: Simulieren Sie Regen, Schnee und Beulen, um die Signalstabilität zu überprüfen.
6. Intelligente Fertigungstechnologie für Automobildrahtgürtel
- Automatisierter Prozess für die Bearbeitung von Drahtgärten: Die vollautomatische Schneid - und Crimpmaschine verfügt über eine Genauigkeit von ± 0,1 mm und eine tägliche Produktionskapazität von 2000 Sätzen.
- Automobilmontagefehlerverhütungssystem: Mit RFID-Technologie zur Überprüfung von Drahtgürtcodes wurde die Montagegenauigkeit auf 99,97% verbessert.
Schlussfolgerung
Von den Konstruktionsspezifikationen für Hochspannungsdrahtgurte in neuen Energiefahrzeugen bis hin zu EMC-Lösungen für intelligente Fahrdrahtgurte entwickelt sich das Layout-Design von Automobildrahtgurten in Richtung Leichtgewicht und hohe Integration. Die Beherrschung dieser Schlüsselelemente der Anbindungstechnologie für elektronische Systeme in der Automobilindustrie wird die Qualität der Fahrzeugentwicklung und die Wettbewerbsfähigkeit auf dem Markt effektiv verbessern.