管理者による
2025-03-19 01:12:40
自動車配線ハーネス設計のコアポイントとエンジニアリング実践
配線ハーネスの設計は、車両の安全かつ効率的な電気接続を保証する重要なエンジニアリングプロセスです。
車載電子システムの統合設計の重要なリンクとして、車載配線ハーネスのレイアウト設計は、車両全体の電気性能と信頼性に直接影響します。自動車の「ニューラルネットワーク」として、配線ハーネスは複雑な環境でのオンボード電子機器の効率的な接続ソリューションを実現する必要があります。以下では、設計原理から製造工程全体までの技術的ポイントを詳細に説明します。
1.自動車配線ハーネス設計の基本原則
- 安全設計仕様 :レイアウトは、防火、耐熱性、耐湿性の要件を満たし、短絡や接地障害のリスクを回避する必要があります。
- 車両 配 線 ハー ネ スの 信頼 性 保証 : - 40 ° C の 過 酷 な 作業 条件 に 適応 するために 、 耐 高 温 および 耐 振 動 ワイ ヤ を選択 します〜 125 â.
- 自動車用配線ハーネスの軽量レイアウト : 配線ハーネスの長さとジョイントを簡素化し、故障率と後のメンテナンスコストを削減します。
- メンテナンス性エンジニアリング規格 : モジュラー設計を採用し、迅速なメンテナンスのためにカラーコードラベルとペアリング。
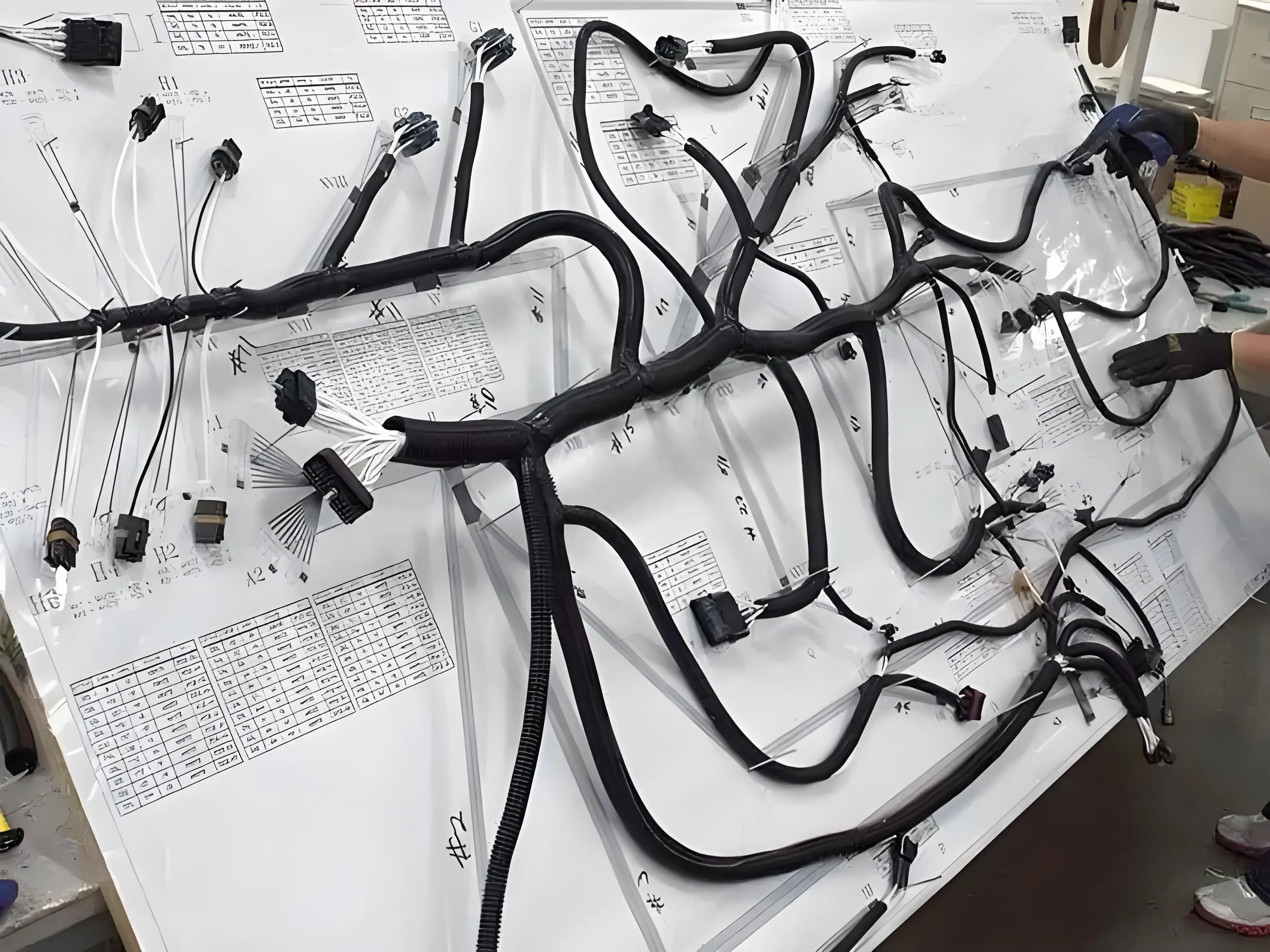
2.自動車配線ハーネスレイアウト戦略の最適化
- パーティション配線設計方法 : 信号の交差干渉を避けるために、エンジンコンパートメントやキャブなどの領域に独立した配線を使用します。
- 電磁適合性保護技術 : 高周波信号線は二重シールド層を使用し、電力線から少なくとも 15 cm の距離を維持します。
- 新エネルギー自動車配線ハーネスの軽量ソリューション : アルミニウムワイヤと薄肉絶縁材を使用し、従来の銅ワイヤと比較して 30% 軽量化。
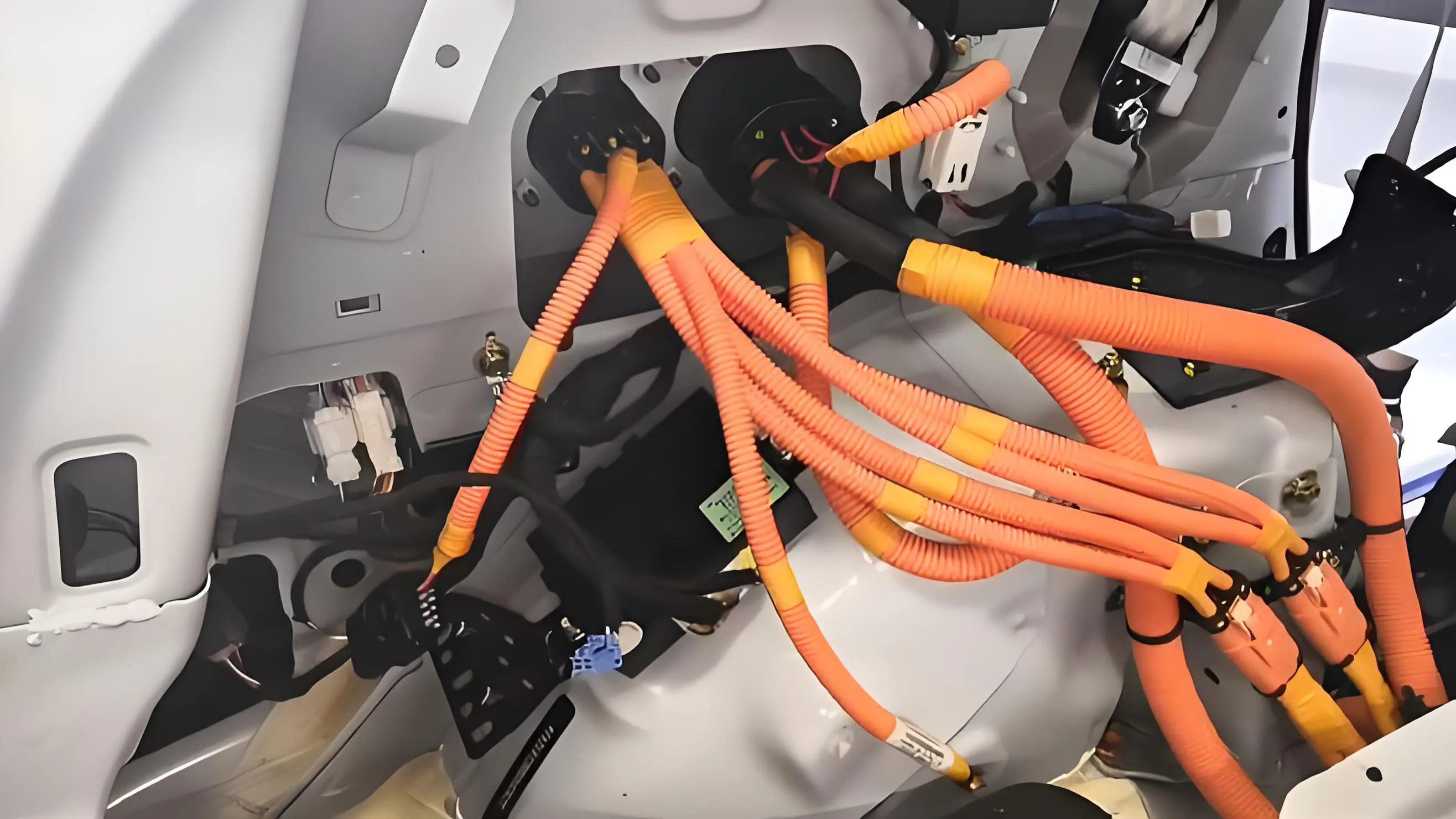
3.自動車用配線ハーネスのコアコンポーネントの選定要点
- 自動車用配線ハーネスのワイヤ仕様の計算 : 負荷電流に基づいてワイヤ径を合わせます ( 例 : ABS に必要な断面積 2.5 mm 2 ) 。
- 自動車用コネクタの防水設計 : 振動の緩みを防ぐスナップオン固定付きの IP67 グレードのシールコンポーネント。
- 新エネルギー自動車の高圧配線ハーネス材料: シリコーンゴム絶縁層は 300 °C の高温に耐えることができますそして 800 V 電圧プラットフォームの要件を満たします。
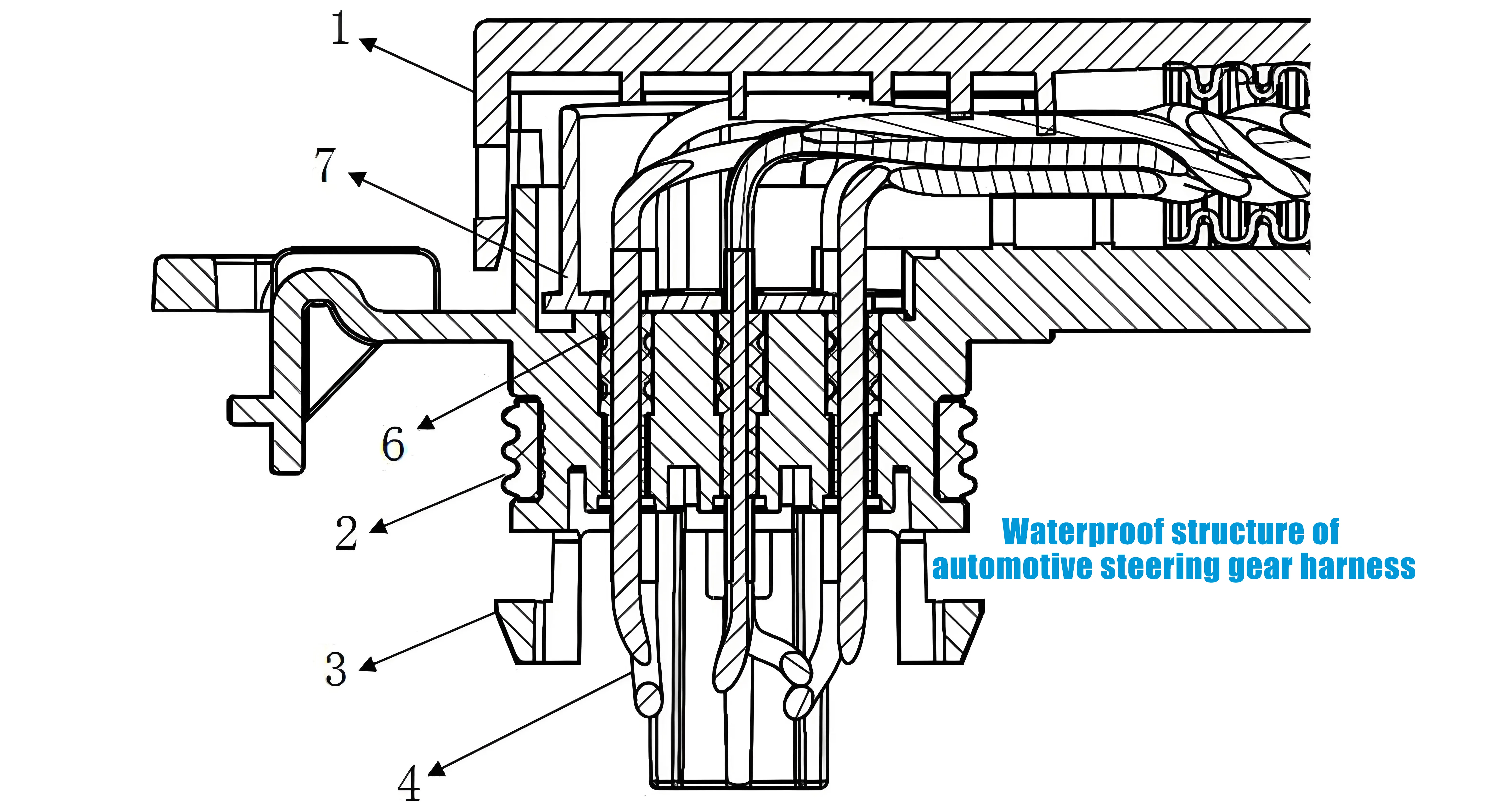
4.自動車配線ハーネスレイアウトの完全なプロセスステップ
- 車両電気システムの要件分析 : ECU やセンサーなどのデバイスの消費電力と通信マトリクスを確立します。
- 3D 配線ハーネスのルーティングシミュレーション : CATIA / CHS ソフトウェアを使用して、経路の合理性を検証し、可動部品からの干渉を回避します。
- ワイヤハーネスサンプルの信頼性検証 : 100000 挿入および抽出試験および 50 G 機械的衝撃試験などの厳格な実験を通じて。
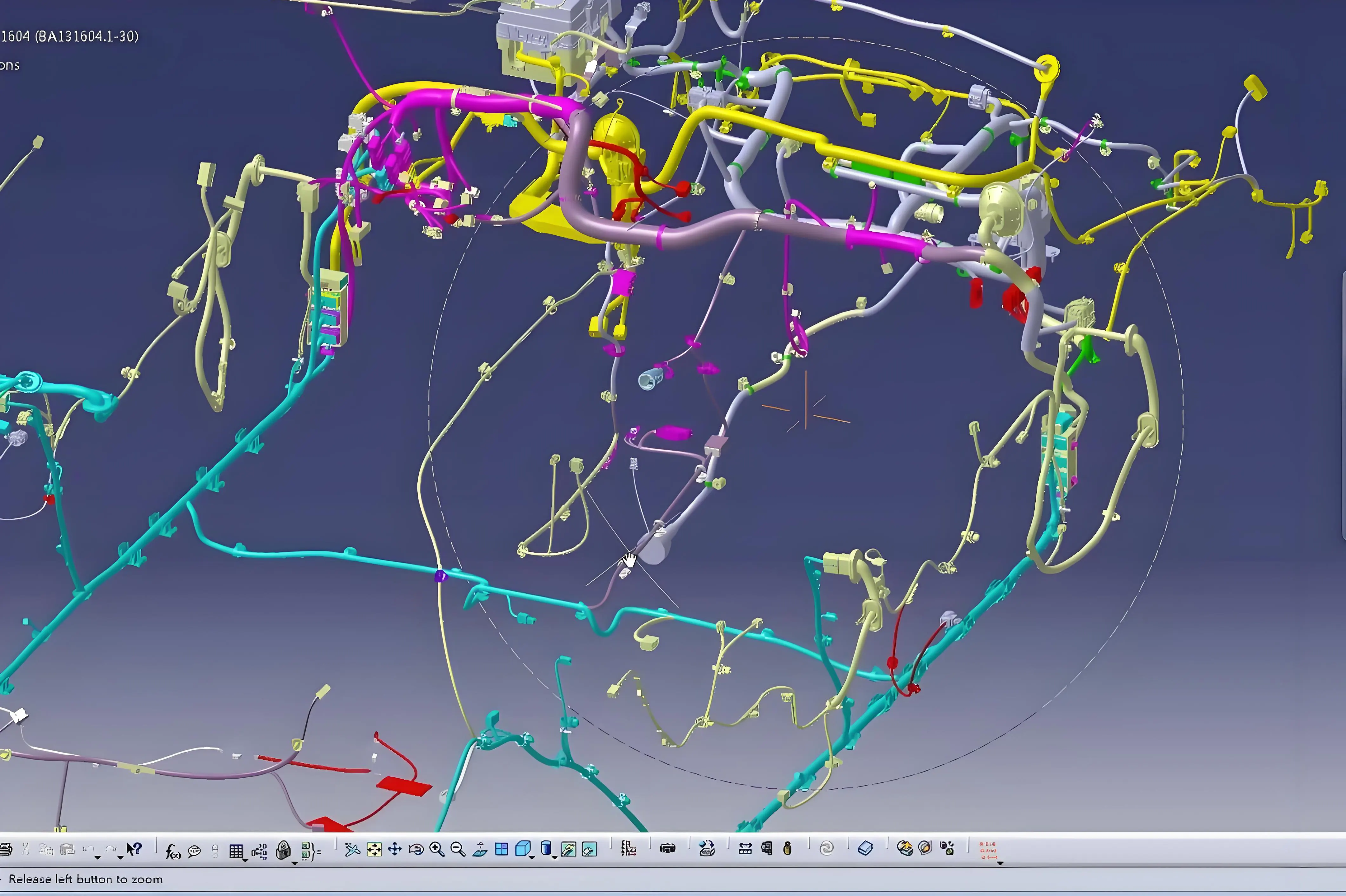
5.自動車配線ハーネス試験の重要なステップ
- 導電インピーダンスの自動検出 : フライングニードルテスターを使用して 100% の回路連続性スクリーニングを達成します。
- 高電圧ワイヤハーネス絶縁性能試験 : 500V DC は漏れ電流 < 10mA で 60 秒間耐える電圧試験に耐えます。
- 車両電気システムのジョイントデバッグテスト : 雨、雪、バンプをシミュレートして信号の安定性を検証します。
6.自動車用配線ハーネスのインテリジェント製造技術
- ワイヤーハーネス加工の自動化プロセス : 全自動切断 · クリミングマシンは ± 0.1 mm の精度と 2000 セットの 1 日生産能力を持っています。
- 自動車組立エラー防止システム : RFID 技術を使用してワイヤハーネスコードを検証し、組立精度を 99.97% に改善しました。
結論
新エネルギー自動車の高電圧配線ハーネスの設計仕様から、インテリジェントドライビング配線ハーネスの EMC ソリューションまで、車載配線ハーネスのレイアウト設計は軽量で高集積化に向けて進化しています。これらの車載電子システム接続技術の要点を習得することで、車両開発の質と市場競争力を効果的に高めることができます。