By Admin
2025-07-15 00:58:45
M25 Waterproof USB Aviation Connector Harness
M25 waterproof USB aviation connector harness, with IP67/68 waterproof rating, excellent electrical performance, and mechanical reliability, is suitable for a variety of environments and is widely used in industrial, outdoor, communication, and other fields; In the digital age, the stability of transmission equipment directly affects industrial efficiency, communication quality and intelligent system response speed. Industry data shows that 38% of transmission equipment failures are caused by material defects in core connection components, and 29% are caused by process errors. However, our USB2.0 M25 connector, through strict material selection and precision manufacturing, controls the failure probability to less than 0.2%, becoming a reliability benchmark in the transmission field.
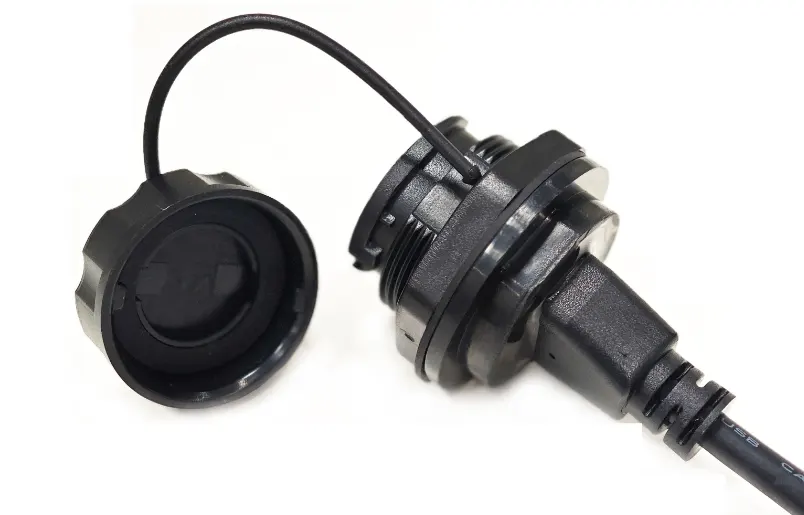
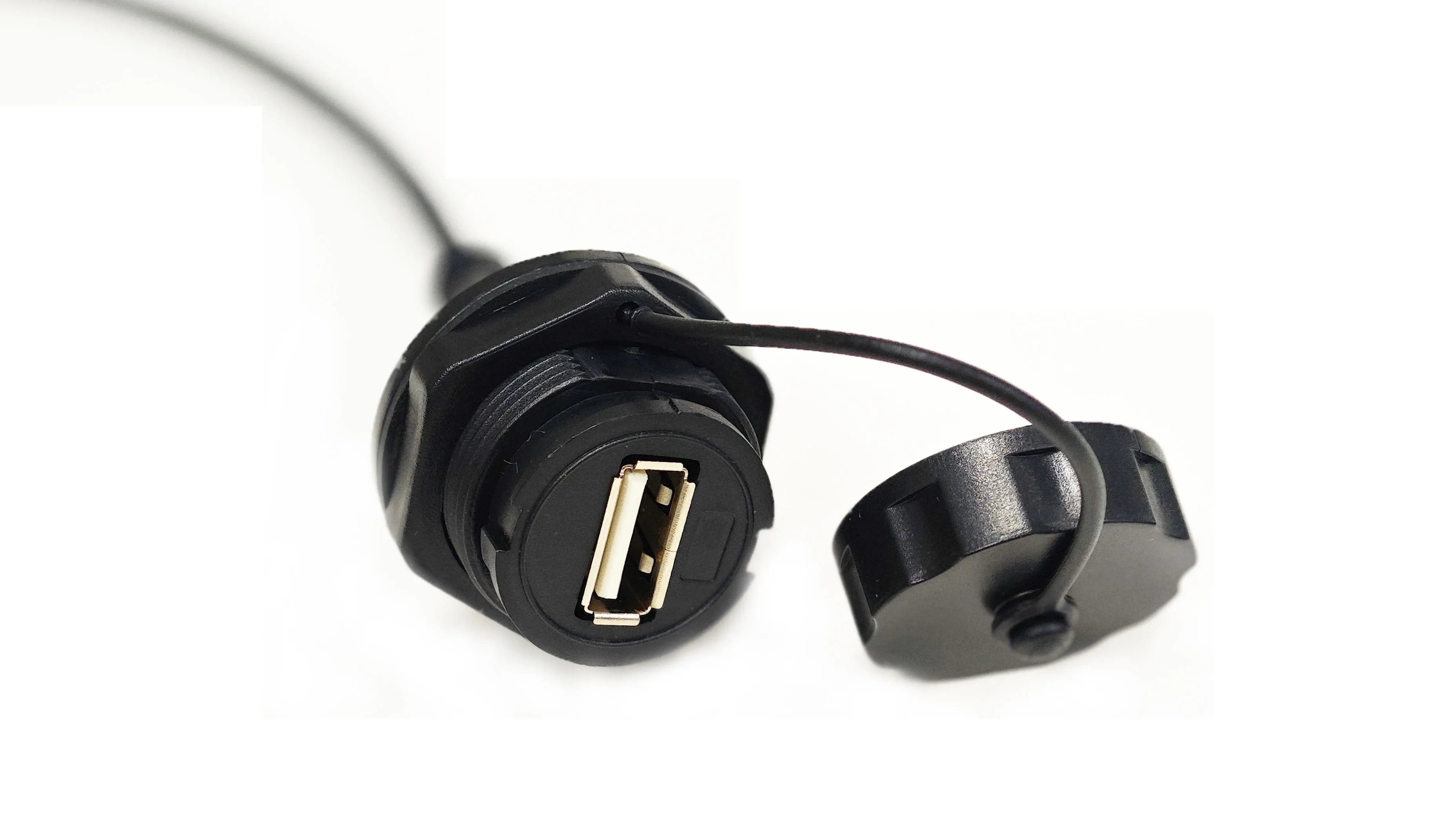
1. Selected materials: performance limits supported by data
Wire material:
The core wire of this product adopts UL2725 28AWG/1P + 24AWG/2C, and each parameter has been verified by engineering:
- Conductor material: We use 99.9% high-purity oxygen-free copper with a conductivity of 101% IACS, which is 15% lower than the transmission loss of ordinary electrolytic copper. The 28AWG wire diameter is twisted by 7 strands of 0.12mm copper wire, with a single strand tolerance of ±0.003mm and a continuous current carrying capacity of 0.8A at 30°C; the 24AWG wire diameter is twisted by 7 strands of 0.20mm copper wire, with a current carrying capacity of 2.5A, which can meet the signal and power supply requirements of the transmission equipment.
- Insulation and outer covering: The inner insulation layer is made of 105°C temperature-resistant PVC with a breakdown voltage ≥20kV/mm; the outer black sheath is modified PVC, which can withstand extreme temperature cycles from -40°C to 80°C (1000 cycles without cracking), and has wear resistance of 5000 frictions under a load of 500g without exposing copper (in compliance with ASTM D4060 standards).
Connector:
Every design of the connector is aimed at "zero failure", and the key parameters are as follows:
Tail end components:
- DuPont 2.54 plastic shell (4pin): reinforced nylon 66 + 30% glass fiber, tensile strength 85MPa, dimensional stability at -40℃ to 105℃ (thermal deformation ≤0.2mm/m), passed UL94 V-0 flame retardant test (self-extinguishing within 10 seconds from fire) and needle flame test (IEC 60695, no open flame spread).
- DuPont 2.54 terminal: tin plating thickness 5μm, no rust in 48-hour salt spray test (ASTM B117), plug-in force stable at 3.5±0.5N, crimping force with 24-28AWG wire ≥8N (in compliance with UL486A standard).
Front-end components:
- USB A 2.0 female 4P: phosphor bronze shrapnel (elastic modulus 110GPa), after 1500 plug-in and pull-out tests (speed 30mm/s), the initial contact resistance is 26mΩ, and after the test, it is still ≤30mΩ, and the data transmission bit error rate is low.
- M25 waterproof connector: PC+ABS black shell, IP67 waterproof level (immersion in 1 meter water for 30 minutes), with black silicone sealing ring (ozone aging resistance), hardness 60±5 Shore A, compression permanent deformation rate ≤15% (100℃×22 hours), can still seal in 10-2000Hz vibration environment, suitable for Φ12-18mm cable installation.
2. Rigorous craftsmanship: millimeter-level precision throughout the manufacturing process
Each product is precisely controlled at each process, and the quantitative standards for key processes are as follows:
- Wire cutting: A fully automatic wire cutting machine is used, with the length error controlled at ±0.1mm (upgraded from the original ±0.5mm), an hourly production capacity of 3,000 wires, and a cutting surface verticality of ≥90°±0.5° to avoid subsequent welding deviation.
- Stripping and core stripping: After cutting off the braided aluminum foil, the outer sheath stripping length error is ≤0.2mm, and the exposed length of the core wire stripping head is 3.0±0.1mm. Ensure that the core wire is not crushed after stripping (no copper wire is broken under a microscope).
- Welding wire: pulse hot pressing welding process is adopted (temperature 380±5℃, pressure 0.3MPa), the pull-off force of the solder joint is ≥5N (industry average 3N), and the insulation resistance after welding is ≥1000MΩ (500V DC), eliminating signal interruption caused by cold soldering.
- Molding inner and outer molds: The injection molding machine is controlled by a servo motor, the inner mold injection pressure is 80±2bar, the outer mold uses 45P PVC, the impact strength at -30℃ is 20kJ/m², and the volume change rate is ≤5% after testing with IRM 903 oil (70℃×24 hours), and the mechanical impact resistance is strong. The outer mold cooling time is 15±1 seconds, and the dimensional accuracy after molding reaches IT12 level (tolerance ±0.05mm), and the clearance with the joint is ≤0.03mm.
- Pouring AB glue: As shown in the figure below, use a fixture to automatically mix at a weight ratio of 1:1 (error ≤±1%), 2 hours for initial solidification, and 24 hours for full solidification at 25℃. The thermal conductivity of the glue after curing is 0.8W/(m・K). In the -50℃ to 120℃ cycle test, the waterproof sealing performance remains unchanged for more than 5 years.
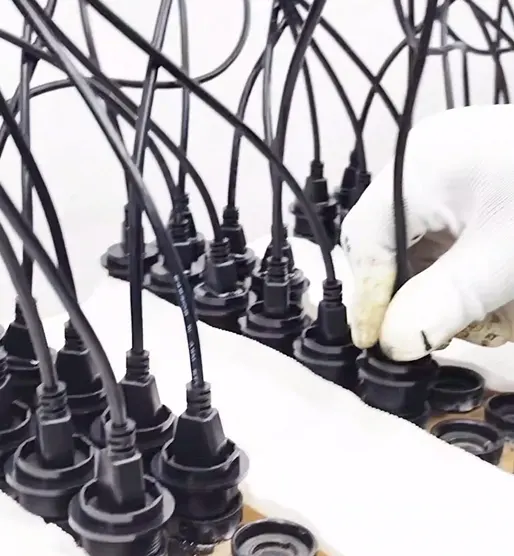
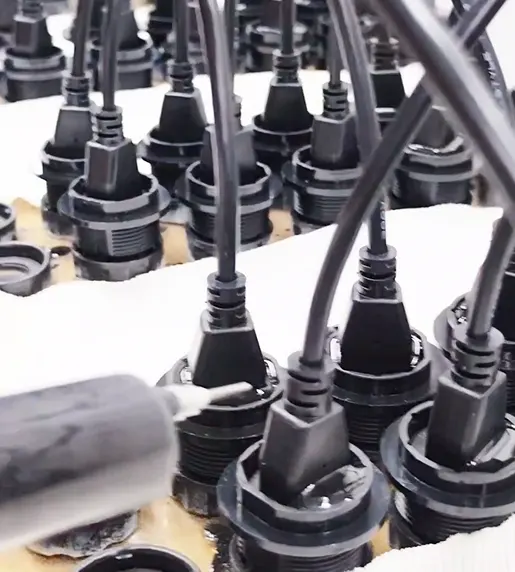
- Insert the casing and tail end processing: insert a 600V, 5.0mm diameter, 30mm long black casing into the tail end of the wire, insert the DuPont rubber shell after the terminal is made, and then shrink the casing.
Testing session:
- Electrical test: continuity test (resistance ≤ 1Ω), insulation test (≥ 100MΩ at 500V DC);
- Mechanical test: 180° swing test (frequency 1Hz, stroke 50mm) still conducts normally after 3000 times. During the test, the product is fixed on a special fixture, and the cable swings back and forth in a 180° range. The on-resistance change is ≤0.5Ω (much lower than the industry average 1Ω standard), and the connector has no cracks, and the wire is not broken, verifying the structural stability under high-frequency shaking scenarios. After the test, the appearance will be 100% inspected.
Technical focus:
- External mold molding: Using 45P PVC material, it has UV resistance, the molding efficiency is 20% higher than that of traditional materials, and the surface finish reaches Ra0.8μm, with excellent overall aesthetics.
- Molded SR: The tail end of the connector is made of a stress relief structure (SR), which can disperse the stress when the cable is bent, and increase the number of swing tests from the conventional 2000 times to 3000 times, greatly reducing the risk of cable breakage.
From the molecular-level control of materials to the micron-level precision of processes, the USB2.0 M25 connector cable produced by Kaweei Harness Factory has redefined the reliability standards of the core components of transmission equipment. Whether it is industrial control in extreme environments or high-frequency interactive communication networks, it can become the key support for "zero compromise" in your transmission link. If you need a customized harness, don't hesitate to get in touch with us.