By Admin
2025-07-12 06:55:43
XT60 Connector Cable
In the field of DC power connection, safety and reliability are the core demands. Today, we grandly launch the Middle HB PN:230-0002 DC Cable, which is based on UL certification and supported by precision technology. It is equipped with XT-60 connectors at both ends, which are easy to plug and unplug and stable. The main line adopts a high-performance connection cable with a UL1015 12AWG red and black double-wire design that has good conductivity and can easily distinguish between positive and negative poles. It is specially designed for high-stability DC power supply scenarios, and fully interprets the core value of "safe connection" from materials to craftsmanship.
Middle HB 230-0002 is a cable dedicated to DC power transmission. Its core parameters are designed around "safety" and "durability", and its safety performance indicators are outstanding: both ends are UL-certified XT-60 plugs, and the asymmetric plug-in and plug-out fool-proof structure meets UL safety standards and can prevent reverse polarity. The contacts are made of high-purity nickel-plated brass with a conductivity of ≥90% IACS, ensuring low resistance and low heat generation; the main line is a UL1015-certified 12AWG red (positive) and black (negative) double wire, which is twisted with 105 strands of 0.25mm copper wire, with a rated voltage of 600V DC and a temperature range of -40℃~105℃, which can meet the high current transmission requirements of continuous current carrying of 30A and peak current carrying of 60A;
The outer layer has a nylon braided mesh tube with a tensile strength of ≥20N to prevent wear, and the surface is covered with a heat shrink tubing printed with "DC Cable, Middle HB PN:230-0002" for easy traceability and identification. Its excellent performance is derived from the ultimate control of the production process, starting from ensuring the stability of subsequent welding and assembly, and cutting wires with millimeter-level precision. The 6 core processes are linked together, and each step is a commitment to quality.
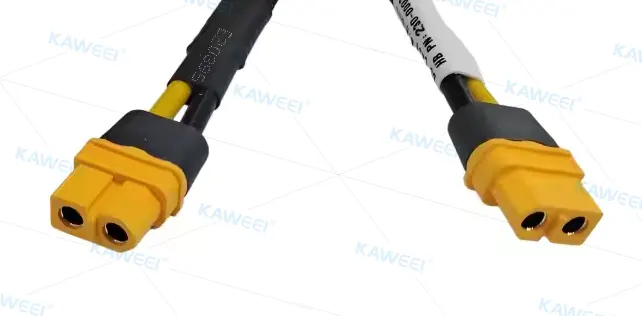
1. Wire cutting: millimeter-level precision length control
- Use a fully automatic wire cutting machine (accuracy ±0.1mm) to accurately cut UL1015 12AWG red and black double wires according to the designed length (customizable). After cutting, the wire ends are flat and burr-free (to avoid puncturing the insulation layer and causing a short circuit);
- Immediately after cutting, the wire diameter and appearance are checked by a visual inspection system to ensure that the wire is not damaged or indented and meets the UL1015 requirements for the integrity of the insulation layer.
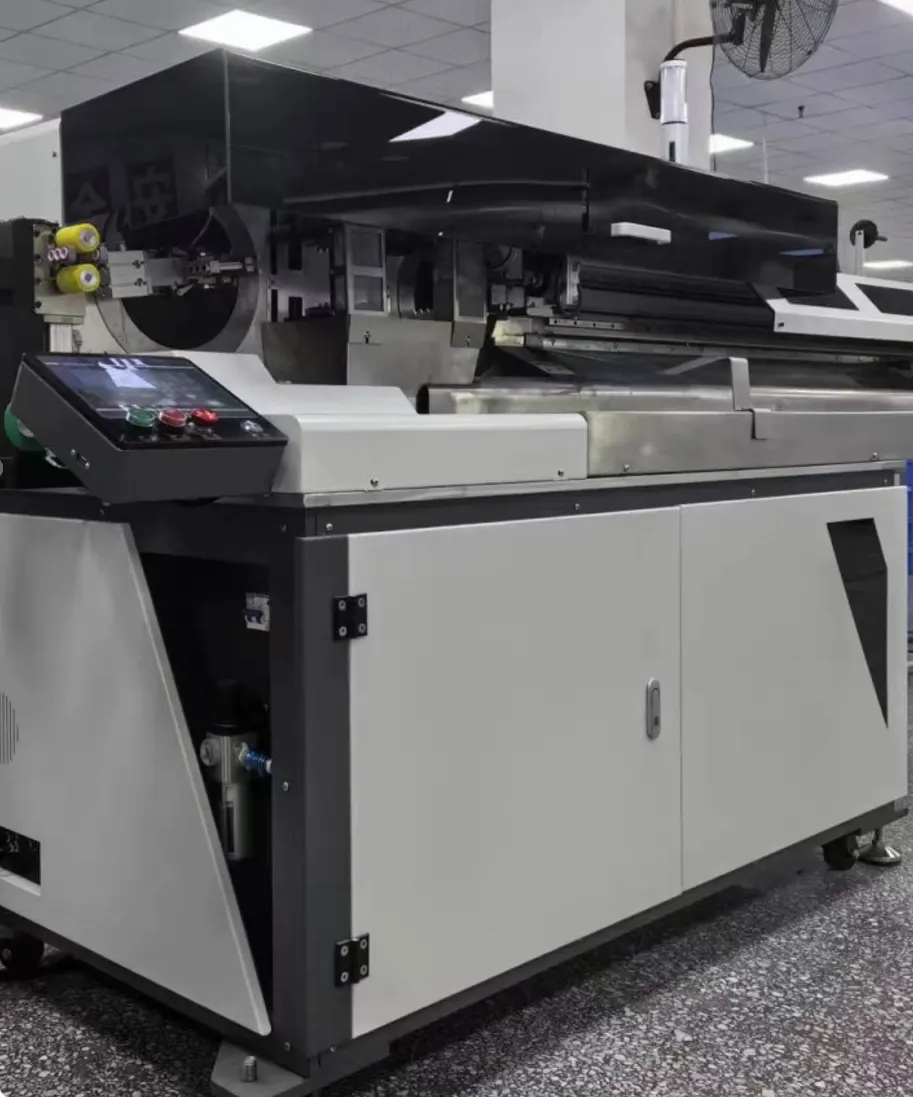
2. Stripping: Layered processing to protect the conductor and insulation layer
- The stripping length of the outer insulation is accurate to 3mm (error ≤0.5mm), ensuring that the exposed conductor length fits the welding position of the XT-60 connector.
- During the stripping process, the conductor is prevented from being scratched (copper wire breakage rate ≤0.1%) to ensure that the current carrying capacity is not affected.
- After stripping, the integrity of the copper wire is quickly tested by the secondary element to eliminate the risk of wire breakage caused by improper stripping.
3. Welding: high-temperature welding to ensure electrical continuity
- Preparation before welding: twist the stripped copper wire into a bundle (to prevent loose wires)
- Welding process: use an automatic constant temperature soldering machine (temperature setting 380±10℃, in line with UL's safety limit for welding temperature), accurately align the copper wire with the contact, and complete the welding at a speed of 0.8 seconds/point, with a solder coverage rate of ≥95%, forming a solid metal welding layer;
- Inspection after welding: visually check whether there are bubbles inside the solder joint (to prevent false solder joints), and use a tensile tester to test the tensile strength of the solder joint (≥5N, to ensure that it does not fall off under vibration).
4. Mesh pipe: strengthen structural stability, prevent loosening, and wear
- ITosolve the problems of "loose wires" and "wear" in long-term use of cables, the mesh tube threading link is an important protective measure:
- Use a nylon braided mesh tube (diameter 8mm, length 430mm, suitable for 12AWG double wire) with a temperature resistance of ≥125℃, and use an automatic tube threading machine to wrap the red and black double wires as a whole, leaving 10mm at both ends of the mesh tube for subsequent fixation;
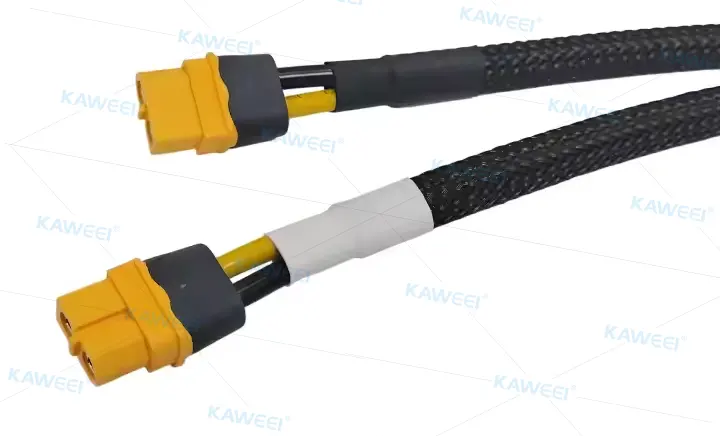
5. Printed sleeve and baking sleeve: clear marking and upgraded protection
Printed sleeve and baking sleeve: Use UL-certified heat shrink sleeve (temperature resistance 105°C), print "DC Cable, Middle HB PN:230-0002" clearly with a printer (diameter 9mm, length 28mm, font size 3, zoom 1, clarity ≥99%), put it on the left end of the cable, and heat and shrink it in a baking oven (100°C) to ensure that the label does not fall off;
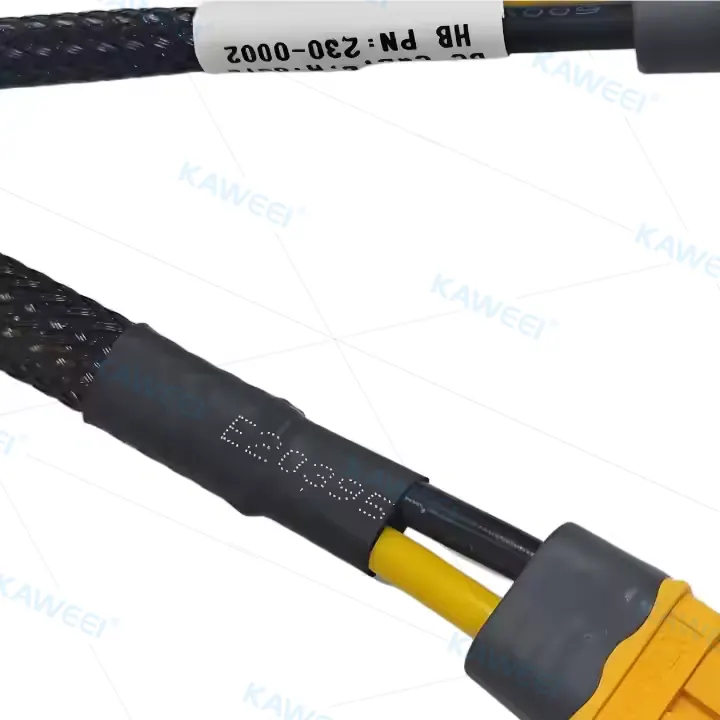
6. Continuity test: 100% full inspection to eliminate safety hazards
- Each Middle HB PN:230-0002 DC Cable must pass a strict continuity test before leaving the factory, and use precision instruments to check whether the positive and negative poles are unobstructed - the red wire is connected to the yellow positive contact of the XT-60, and the black wire is connected to the black negative contact, ensuring that the conduction resistance is ≤50mΩ (far lower than the 100mΩ safety limit specified by UL), so that the electrical performance is fully compliant. This cable with UL-certified safety genes and precision craftsmanship has a wide range of applications.
- Middle HB PN:230-0002 DC Cable is suitable for heating machines, industrial DC power supply equipment (such as server power supply, internal connection of charging piles) and energy storage systems (connection between lithium battery packs and inverters). From millimeter-level precision in wire cutting to 100% inspection of conduction test, it redefines the safety standard of DC connection cables with the dual protection of "UL certification + precision technology". Choosing it means choosing a "zero hidden danger" power connection experience - safety starts from every detail.