By Admin
2025-07-17 02:41:54
208130-1 Circular Connector Harness Construction Guide
The 208130-1 circular connector harness is a key component commonly used in the field of electrical connections. It has many pins or contacts and can transmit power, signals, or data. It is cylindrical. In the signal and power transmission system of electronic equipment, its quality directly affects the operating efficiency and service life of the equipment. The TE AMP 208130-1 connector harness is excellent in materials, manufacturing process, and performance. Let's talk about it with specific data from these three aspects.
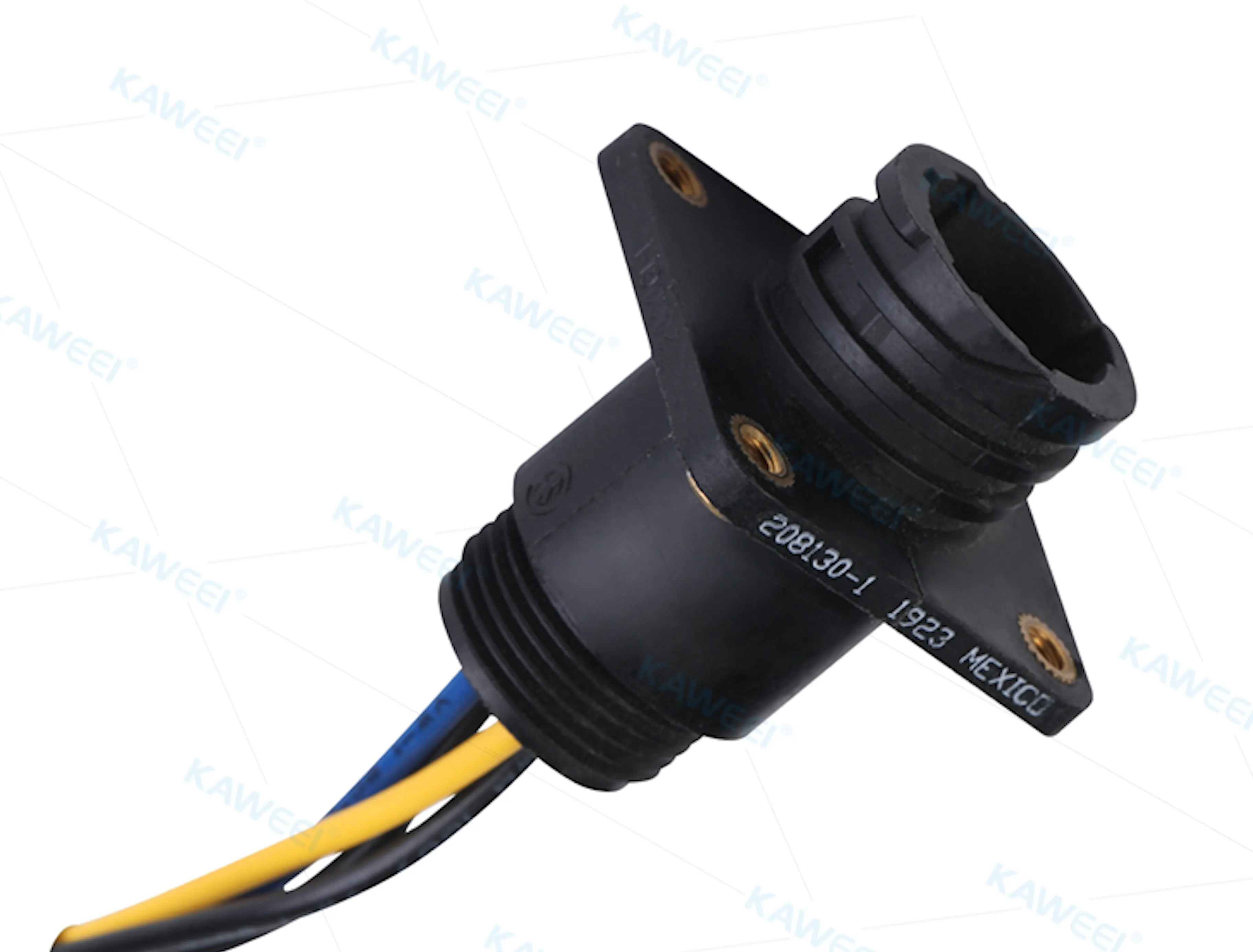
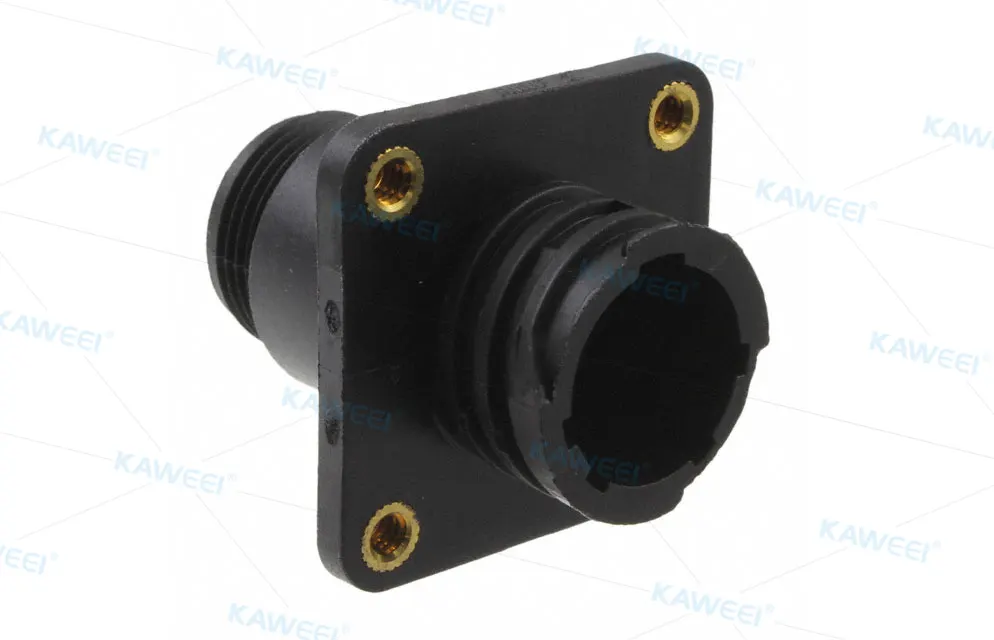
1. Core materials: accurate material selection to build a stable connection foundation
UL1007 20AWG Wire
- Conductor material and performance: The conductor is made of 99.99% pure oxygen-free copper with a DC resistance of 0.031Ω per meter at 25°C, which is about 11.4% lower than the conductive loss of ordinary copper conductors with a purity of 99.9% and a resistance of 0.035Ω per meter. It can efficiently transmit electrical signals and reduce energy waste. In the test of continuous transmission of 10A current for 24 hours, the surface temperature of the wire rose by only 8°C (ambient temperature 25°C), which is far lower than the 80°C tolerance temperature limit specified by the UL1007 standard.
- Insulation layer characteristics: The insulation layer is made of high-quality PVC material with a thickness of 0.22mm. In the 600V AC withstand voltage test, there is no breakdown or flashover for 1 minute, and the insulation resistance is stable at more than 1000MΩ. After high and low temperature cycle testing (-40℃ to 85℃, 50 cycles), the insulation layer has no cracking or deformation, and the insulation performance retention rate is 95%, which is suitable for a variety of complex environments.
TE AMP Series 208130-1 4PIN Circular Connector
- Mechanical structural strength: The shell is made of thermoplastic (nylon + 30% glass fiber). After the drop ball impact test (1kg steel ball falls freely from a height of 1m), the shell is not broken. In the plug-in life test, after 5000 cycles, the plug-in force change rate is <10% (initial insertion force 8- 12N, pull-out force> 5N), ensuring a long-term stable connection.
- Electrical connection performance: After the salt spray test (5% NaCl solution, temperature 35℃, 48 hours), the contact resistance increased from the initial 3mΩ to 5mΩ, with a change rate of less than 70%, which is much better than the industry average (the contact resistance change rate of most connectors after the salt spray test exceeds 100%). The rated current carrying capacity is 3A, and when the 3A current is continuously transmitted, the contact temperature rise is less than 5℃.
4PIN MOLEX 4.2mm plastic shell
- Dimensional accuracy and adaptability: The plastic shell adopts high-precision injection molding technology, and the dimensional tolerance is controlled at ±0.03mm. After sampling and testing 100 plastic shells, the pin spacing error is less than 0.02 mm, and the adaptability with UL1007 wire is 100%. This ensures that wires with riveted terminals can be accurately accommodated without sticking or loosening.
- Material environmental resistance: The shell is made of high-temperature resistant PA66 nylon. After thermal aging test (continuous operation for 1000 hours at 105℃), the tensile strength retention rate is 80% and the impact strength retention rate is 75%. In the humid environment test (humidity 95%, temperature 40℃, continuous 100 hours), the insulation performance has no obvious decline, and the insulation resistance is still greater than 500MΩ.
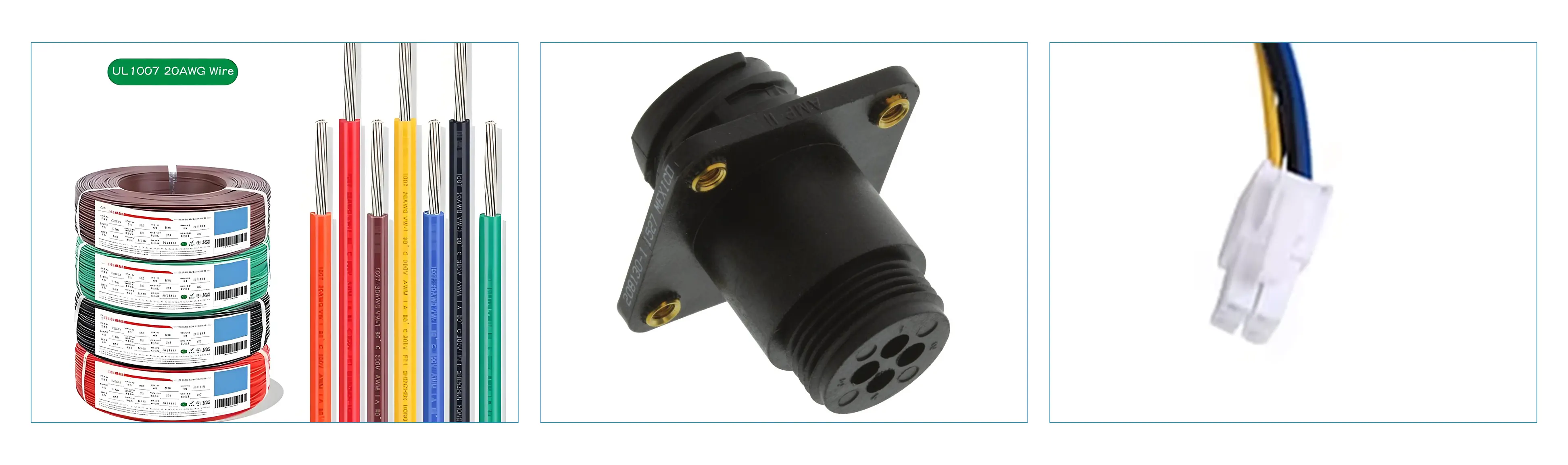
2. Production process: fine control
Cutting line:
- Fully automatic wire cutting machine equipped with a high-precision laser distance measurement system.
- The length error is controlled within ±0.2mm, of which 98% of the wire length error is within ±0.1mm, which is much higher than the industry standard of ±0.5mm.
- 5,000 wires can be cut per hour, and the production efficiency is 60% higher than that of semi-automatic equipment.
Stripping:
- The pneumatic stripping machine uses a high-precision cylinder with a pressure adjustment range of 0.3-0.6MPa. It can accurately control the stripping force according to the wire specifications, and the stripping blade gap adjustment accuracy is ±0.01mm.
- The front-end stripping length is accurately set, and the stripping length error is within ±0.1mm for 99%, and the maximum error does not exceed ±0.2mm; the tail-end stripping length error is within ±0.1mm for 98.5%, which meets the requirements of subsequent tinning and riveting terminals.
Tin plating:
- The double-head tinning machine adopts a constant temperature heating system with a temperature control accuracy of ±2℃ and a tinning time adjustment range of 0.5-3 seconds. It can connect two wires at the same time.
- The soldering temperature is stable at 265±5℃, the welding time is controlled at 2-4 seconds, and the bonding area between the tin point and the conductor is greater than 90%. The tensile test shows that the pull-off force of the tin point is greater than 3N, which is much higher than the industry standard (most requirements are greater than 2N), ensuring that the wire and the terminal are firmly welded.
Rivet terminal:
- The automatic terminal machine adopts a servo drive system, with a pressure control accuracy of ±1N and a riveting stroke adjustment accuracy of ±0.01mm, which can achieve precise riveting of terminals.
- For terminals and UL1007 wires, the riveting parameters are optimized with a tolerance of ±0.02mm. After riveting, the contact resistance between the terminal and the wire is less than 0.5mΩ, which is about 30% lower than before riveting, improving the conductivity.
Wear a rubber shell:
- With the help of customized chemical fixtures, the wire is guided to penetrate the 4-pin molex 4.2mm plastic shell accurately, and the positioning error of the plastic shell is less than ±0.05mm.
Sealing glue:
- After the front end is inserted into the TE AMP 208130-1 connector, high-viscosity, waterproof, and dustproof silicone is used for sealing. The thickness of the sealing glue is controlled at 0.8-1.2mm, and the uniformity of the sealing glue is guaranteed by the coordinated control of the pressure sensor and visual inspection.
- After sealing, the tensile test is carried out, and the wire pull-out force is greater than 6N, which can effectively resist external force pulling. After the IP67 protection level test (immersion in water at a depth of 1 meter for 30 minutes), water does not penetrate the connector, and the protection performance is excellent.
Test:
- Electrical performance test: Using high-precision electrical performance test equipment, conduct a continuity test on each wiring harness, and the conduction resistance is less than 0.1Ω; apply 500V DC voltage, and the insulation resistance is greater than 500MΩ; perform a 2000V AC withstand voltage test, which lasts for 1 minute without breakdown. All electrical performance indicators are better than industry standards.
- Mechanical performance test: tested on a vibration test bench (frequency 10 - 500Hz, acceleration 15g, lasting 4 hours), after the test, the change rate of the wiring harness contact resistance is less than 5%, and the change rate of the plugging and unplugging force is less than 8%; after 1000 plugging and unplugging cycle tests, the contact resistance is stable within 5mΩ, ensuring long-term reliability.
- Environmental adaptability test: After testing in a high and low temperature alternating environment box (-40℃ to 85℃, 10 cycles), the wiring harness has no deformation on the outside and the electrical performance test is qualified; after testing in a dust environment (dust concentration 10g/m³, lasting 24 hours), there is no dust intrusion inside the connector and the performance is normal.
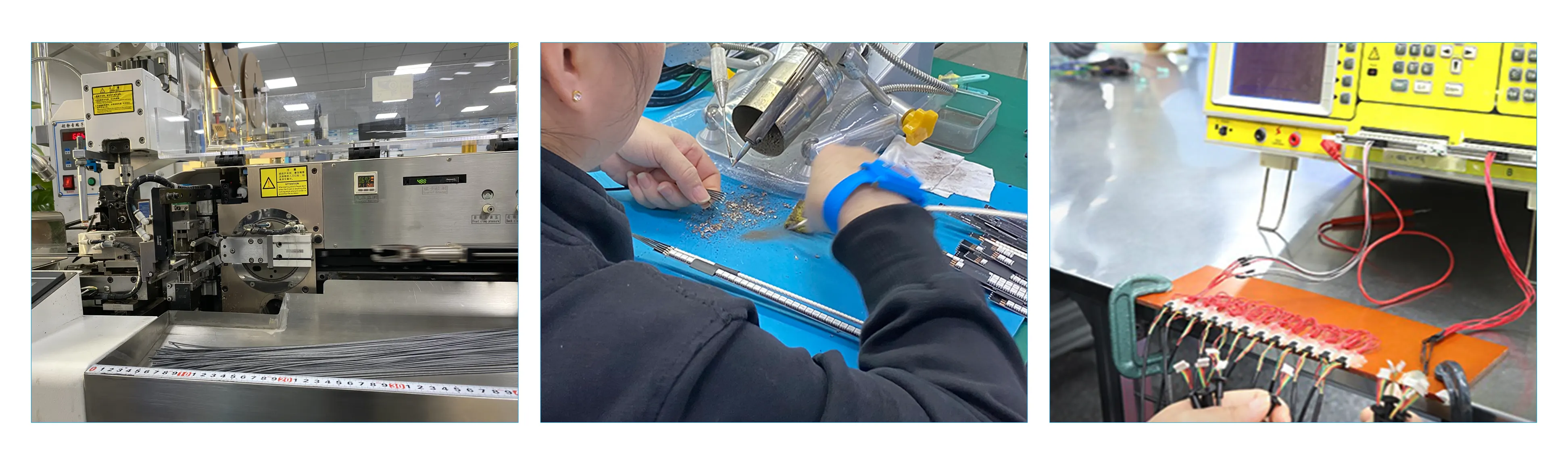
3. Performance Highlights
Signal transmission: "low loss king" in high-frequency scenarios
- In the 100MHz high-frequency test, the signal attenuation rate is only 2.5% (the industry average is 5%-8%). In the intelligent industrial control system, the device response time can be shortened by 10%; when the audio device is connected, the audio distortion is <0.5%, restoring high-quality sound effects.
Lifespan and reliability: Durability in industrial scenarios
- Accelerated life tests (simulating 10 plugging and unplugging times a day and 2 hours of vibration) show that the wiring harness can be used stably for 5-6 years, with a plugging and unplugging life of >10,000 times. In industrial production lines, downtime due to wiring harness failure can be reduced by 24 hours per year (calculated as 2 hours of downtime per month), which is equivalent to a 1.2% increase in production capacity (8,760 hours of annual production time).
Environmental Adaptation: An “All-Round Player” in Extreme Scenarios
- High and low temperature: no performance degradation in -40℃ (cold outdoor) and 85℃ (industrial oven) environments;
- Salt spray: stable use for more than 3 years in a marine climate environment (verified by salt spray test);
- Protection: IP67 waterproof and dustproof, suitable for complex scenarios such as outdoor monitoring, LED, automotive electronics, metallurgical equipment, etc.
TE AMP 208130 - 1 connector harness, from materials to processes, from performance to applications, each is based on accurate data. Kaweei Harness Customization Factory is committed to relying on this high-quality connector harness to provide high-quality and high-reliability solutions for electronic equipment connections. Whether it is industrial automation, automotive electronics, consumer electronics, or outdoor equipment and other fields, it can rely on its advantages to ensure the stable operation of the equipment. If you need to have a deeper understanding of the product's technical parameters and customized services, please contact Kaweei Harness Customization Factory for further communication.