By Admin
2025-07-25 02:35:26
LED Light Harness Production Guide
An LED light harness is a collection of wires used to connect the power supply, control module, and LED lamps in an LED lighting system. It is a key component to ensure a stable power supply and signal transmission of LED lamps. It integrates scattered wires and matches them with insulation sheath, terminals, connectors, and other accessories to form an orderly line bundle, effectively avoiding wire clutter, wear, or poor contact, while simplifying the installation and maintenance process.
In this field, Kaweei's wire harness customization factory, with its professional technical strength and rich experience, can provide customized LED light harness solutions according to the needs of different LED lighting scenarios. Whether it is the requirements for safety and durability in home lighting, or the high and low temperature resistance and vibration resistance required by automotive LED light harnesses, or the strict standards for waterproof and moisture-proof harnesses in outdoor lighting, Kaweei can accurately control and ensure that each customized harness can adapt to the specific application environment, providing reliable guarantee for the stable operation of LED lighting systems.
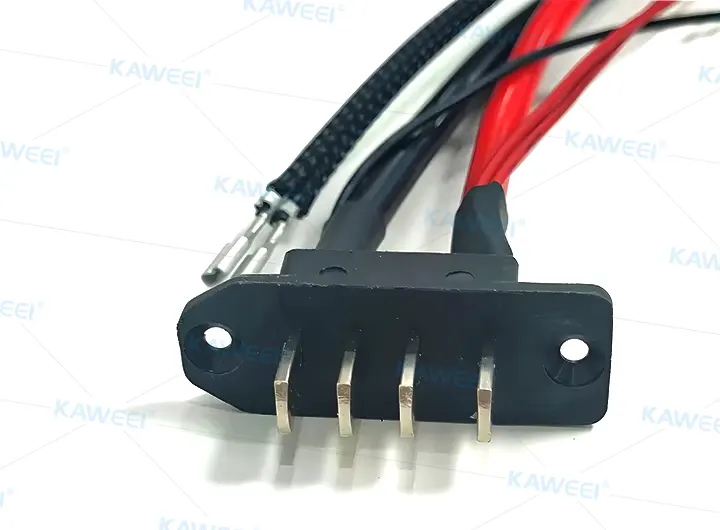
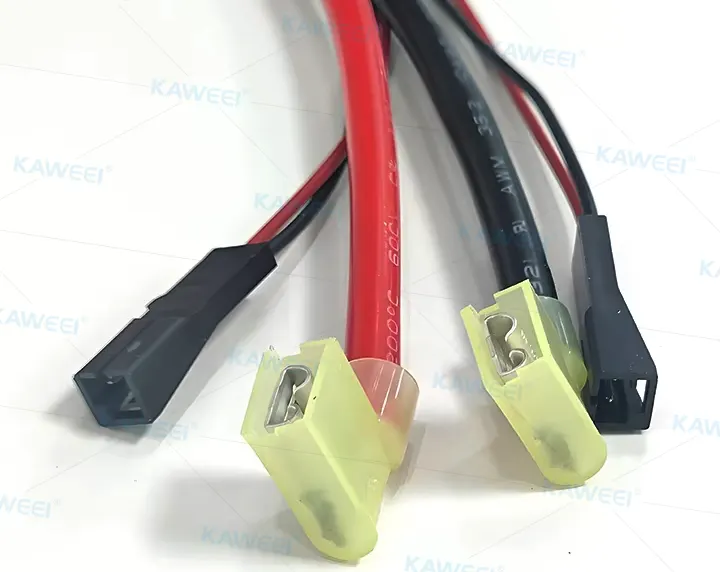
1. Cutting wire:
Wire cutting is the first step in wire harness production and directly determines the stability of subsequent processes.
- The main line uses UL2464 22AWG/2C cable, which is cut into key lengths such as 450±10mm and 440±10mm according to assembly requirements to adapt to the overall structure.
- The branch line uses UL1007 22AWG wire and UL3512 10AWG wire, both cut into 360±10mm to ensure perfect matching with terminals and plug-ins.
We use fully automatic machines to cut wires, which can control the length error within a range of no more than 10 mm. In this way, the subsequent processes can be processed with unified standards.
2. Peeling:
The stripping process is the key to ensuring the conductive performance of the wire harness.
- For UL1007 22AWG wire, the stripping length is 6-8mm to expose the conductor core wire, ensuring effective crimping with the brass continuous 110-pin male terminal flag terminal.
- For UL3512 10AWG wire, the stripping length is 10-12mm, suitable for a 250 flag female terminal, ensuring full contact between the conductor and the terminal.
- The wire end used for welding (such as connecting LED light strips) adopts a half-stripping process (only the outer sheath is stripped, and the core wire insulation is retained) to avoid a short circuit during welding.
3. Terminal Block:
Terminal and cable specifications must be accurately matched:
- 22AWG wire with DuPont 2.54mm terminal, after crimping, must be able to withstand at least 39N of tensile force to be qualified;
- 10AWG wire with 250 flag-shaped female terminal (with yellow insulation layer), after crimping, the tensile force it can withstand must reach at least 356N (this meets the requirements of "crimping pull-off force" on the drawing);
- Testing standard: 3% of each batch of terminals will be randomly selected for tensile testing. If they fail, the entire batch will be reprocessed to avoid power outages or overheating due to poor crimping.
4. Heat shrink tubing:
Do a good job of insulation protection and strictly control the size range. In order to make the insulation effect of the wiring harness better and the mechanical protection more in place, heat shrink tubing will be used. This tubing can withstand a voltage of 600V and has a diameter of 6.0mm. The specific process is as follows:
- Sleeve positioning: Put the sleeve on the terminal crimping place or outside the solder joint, and make sure to cover all exposed conductors.
- Heating process: Use a hot air gun to heat in stages, the temperature is between 120 and 150℃, so that the sleeve can shrink evenly and stick tightly to the wire and terminal. The thickness of the sleeve after shrinking must be at least 0.2mm.
- Dimension control: Strictly follow the requirements of "sleeves and solder joints cannot exceed this plane" on the drawing to ensure that the sleeves and solder joints after heat shrinkage do not exceed the specified plane, and the error is controlled within 0.5mm above and below to prevent them from colliding with other parts during assembly.
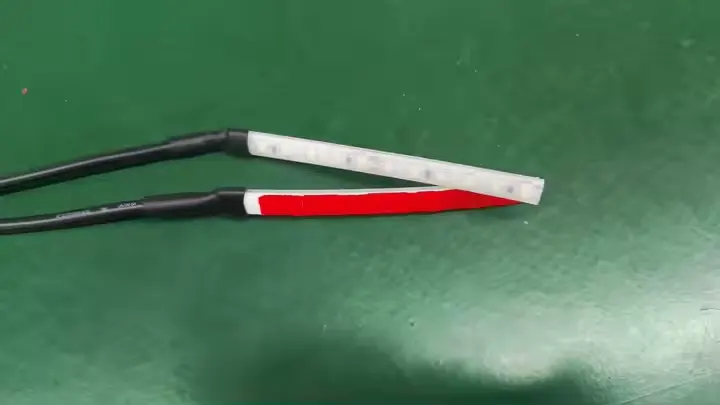
5. Welding light strip:
Whether the LED light strip is welded well or not is directly related to whether the light emission is uniform.
- Welding object: Solder the LED light strip and the UL2464 model 22AWG/2C red and black wires together - the red wire connects to the positive pole ("+"), and the black wire connects to the negative pole ("-"). Before welding, the wire head should be stripped of 3 mm of outer skin to expose the copper core inside before welding.
- Welding technology: The temperature of the electric soldering iron is controlled at around 320℃ (not higher than 330℃, not lower than 310℃), and the welding time of each soldering point should not exceed 3 seconds, so as to avoid the temperature being too high and burning the LED chip.
- Solder point requirements: The soldered points should be in the shape of small water droplets, with a maximum diameter of no more than 1.5 mm, without thorns and without loose soldering; after soldering, use isopropyl alcohol to clean the residual flux.
- Electrical inspection: After soldering, all light strips must be "continuously tested" (check for open circuits or short circuits) to ensure that the light strips and wires are connected smoothly and there is no risk of short circuits.
- In the production of LED light harnesses, every step is strictly carried out by the drawing standards, from the millimeter-level error control when cutting the wires, to the pull-off force test after the terminal connection, to the size supervision of the heat shrink tubing, and the optical inspection after welding.
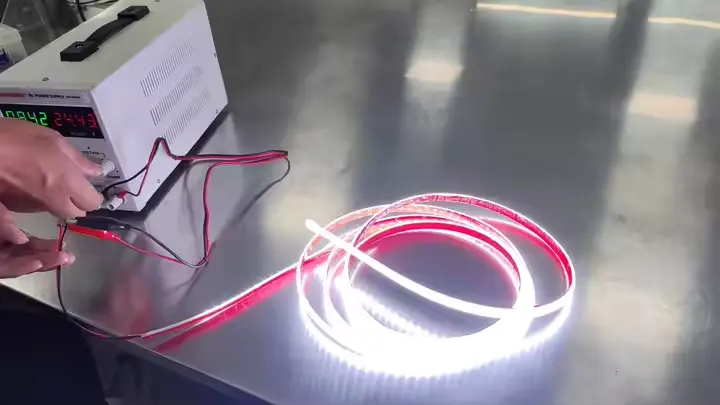
When Kaweei wire harness customization factory produces LED light harnesses, it is precisely this rigorous treatment of every link, from the precise control of millimeter-level tolerances when cutting wires, to the careful pull-off force test of the terminals, from the strict control of the size of the heat shrink tubing, to the meticulous optical inspection of welding, always following the strict standards of the drawings to ensure the quality of the produced harnesses.